Read this first!
As agricultural consultants in California, irrigation consulting during the growing season is our bread and butter. A lot of times, especially in vineyards with lighter soils where I recommend short and frequent irrigations, I know my desired schedule amounts to a tall order. Not everyone can feasibly do two hours, three times a week. No matter what’s best for the vines, I have to work with a human irrigator, who is still going to turn the valve on at 5 pm and turn it off at 7 am the next day.
In a lot of cases, this amounts to a vineyard that is both over- and under-watered: the 14-hour irrigation percolated past the rootzone in under 3 hours and the rest of the week (after the root zone water was depleted) the soil was dry as a bone.
So, I’m happy to see so much interest these days in valve automation.
I’m also apprehensive because I’ve automated valves and it’s not a silver bullet. It’s not any bullet. It’s a useful tool that needs to be applied to what is already a functioning irrigation system. And some of y’all don’t have that.
How does valve automation work?
To get why this is the case, you have to understand how automatic valves are automated. You may have a diaphragm or a bonnet valve in the vineyard already that you manually turn on and off. That valve is then automated via a solenoid, which is a small electromagnetic device with a plunger. When actuated, the plunger moves up to open the valve, or down to close it.
Given that very few farms have line power at valve locations to provide the constant AC power needed to hold open the solenoids, most ag valves use solenoids known as “DC latching solenoids”. They are actuated by ~12V pulses of electric current powered by a solar panel/battery, and held in that position by a mechanical latch. This can be reversed by applying a reverse polarity pulse, in which case the plunger is latched in the opposite state. These actions are triggered by the control system which is ultimately controlled by you via whatever app came with the automating system.
The contact between the solenoid plunger and the actual closing mechanism can be either direct, indirect, or semi-direct (see above video). Most situations you see in vineyards are indirect. The solenoid plunger basically just redirects water from moving on one side of the diaphragm to the other. This creates a pressure differential to open the valve or a pressure equalization to close the valve. The water pressure itself is used to both open the valve and to close it.
This is nice because you can open and close a high water flow valve using only a tiny solenoid plunger actuated with very little energy. The water pressure itself is doing all the work. This is why, for example, a 6-inch valve can be operated using the same solenoid as a 2-inch valve.
The million-dollar question: What if you don’t have enough pressure?
Long story short, your valve isn’t going to open or close the way it should.
To get a more complete answer, I got in touch with Saul Medrano over at AvidWater. Saul has a lot of experience with valve automation in everything from greenhouses to berry farms to vineyards. Vineyards tend to have more challenging topography than other growing situations, so I was interested to hear his opinion on some of the common culprits of dropping pressure in these cases. According to Saul:
“Incorrect usage and placement of air vents is a big one. Some people may think that just because there is an air vent, it’s going to work, but really it depends on what air vent you have and where. That and just not understanding what pressure losses you get across all the components like valves, air vents, filters, check valves. You need to understand what it takes for them to work properly.”
He added:
“You really have to stick to whatever the manufacturer says the valve can handle. If the manufacturer says, ‘Hey, this thing can operate properly at 10 PSI’, it should be able to operate at that.”
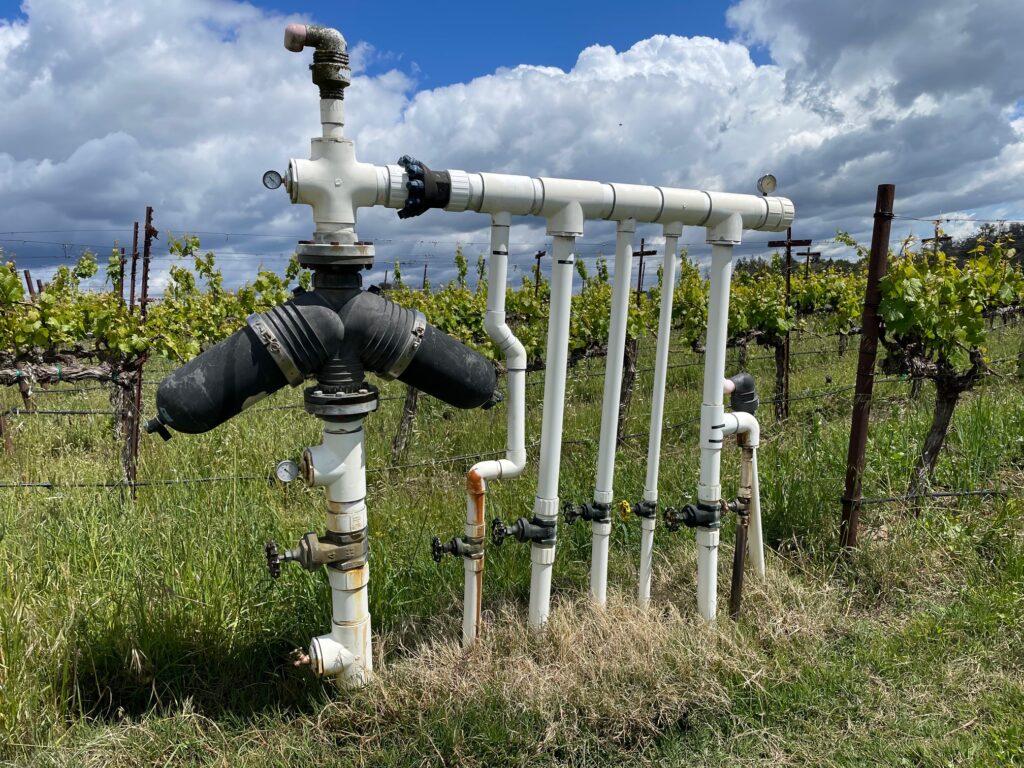
And you may not even have that…
A few years ago, we installed 10 PSI (threshold) pressure switches wherever we had soil moisture probes we monitored to give us irrigation feedback for our weekly recommendations. This was effectively just to measure the duration of irrigations: switch turns on when irrigation starts and turns off when irrigation stops. We chose 10 PSI assuming that people would have at least that in their driplines. For the record, most pressure-compensating drip emitters are designed to function between 12 and 58 PSI. Below (or sometimes above) that range, the emitter output will be erratic and outside the specified flow.
We found in many blocks both hilly and flat, the irrigations failed to actuate the switch. This means that when irrigations get going, the line isn’t even being pressurized to 10 PSI. Aside from issues with distribution uniformity of water and fertilizer, a system like this would need to be automated specifically with valves that could function at low pressure. We’ve often seen automated valves that don’t work consistently because of low system pressure. This usually translates into a valve that doesn’t shut off once it’s turned on because the pressure is too low to impact the diaphragm.
At the source, the pressure these growers are getting is probably adequate. That doesn’t mean that by the time it gets to the valve the pressure is the same. In fact, laws of physics dictate that it is not the same. Filters, fittings, pipes themselves and changes in elevation continually eat away at the pressure you have in your system and that will determine what your options are for automating.
I asked Saul what some of the reasons for poor pressure in vineyards are. He responded:
“Over the last three years, obviously, it’s been a tough market. There are a lot of designs out there that are just designed to be cheaper. Everyone has sacrificed some performance in the system to reduce cost. If your irrigation system isn’t designed properly and you’re not using the right equipment to handle that, low-pressure or high-pressure system, then it’s not going to work.”
And on the other hand,
“I’ve seen some sites where they have all the bells and whistles. They have a VFD (i.e. Variable Frequency Drive) at their pump. They have a pressure-regulating valve at the irrigation site. And then they have pressure-compensating emitters. The diaphragm valve with the pressure-reducing pilot is going to open and close to try to match the pressure that it needs. And in turn, the pressure-compensating emitters are going to do the same thing. You have three things that are trying to achieve this one common goal, and it just creates chaos.”
Most modern irrigation installations I’ve seen have a VFD either installed in tandem or built into the pump control. In the past, VFDs have been incentivized via several government programs (e.g. EQIP, SWEEP). However, just having a VFD isn’t the end of the story. Saul reiterated:
“There’s a misconception that if you have a VFD, you’re going to have the most energy-efficient pumping system. That’s not always true. It may use less energy, but it’s not necessarily going to be the most efficient usage. All it’s going to do is vary the speed of the motor to ramp up or down based on whatever pressure you’re trying to achieve. You need to make sure your VFD is programmed properly in order to have the most efficient energy use that you can have.”
Don’t let me scare you
Saul and I agree that automation is a good thing. With rising labor costs, it’s becoming more of a necessity. It’s also more time efficient when you have to get water to a bunch of blocks in the course of a week. When asked if he had any advice for those thinking of automating, Saul said:
“I think the first thing anyone should do if they’re interested in automation, is do some remote monitoring. Put some sensors on your field and keep track of what’s going on. You can monitor flow, monitor pressure, monitor EC, pH, just know what’s going on now in your field. Then you go into valve control. Now you have control and monitoring. I think everyone should have good data based off a sensor, not from a person who’s subject to human error.”
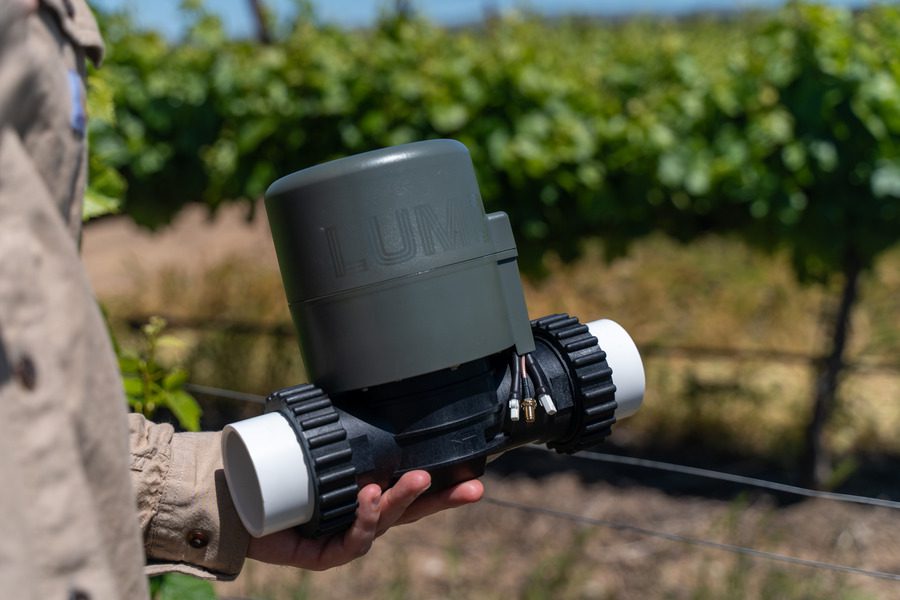
The com-bi-nation valve control and flowmeter
Let’s talk about the new kid on the block, shall we?
Lumo seems to be the latest and greatest in irrigation Agtech and they certainly give us a lot of food for thought. For those who aren’t familiar with the product, Lumo offers an all-in-one valve with built-in flowmeter and telemetry for control and monitoring. Compare this to a more classic automation arrangement where the telemetry device is wired to an external solenoid and (hopefully) a pressure switch (or transducer) to determine whether the valve actually opened and closed when you told it to.
Instead of working via a solenoid, Lumo valves work via a worm drive mechanism that moves up or down when actuated and directs the flow of water over or under the diaphragm. I’ve worked with a couple devices that use this method in place of a solenoid and they seem to perform better in low-pressure systems. Regardless, these valves are specified to operate at between 15 and 80 PSI and I would stick to manufacturer’s specifications…always.
Lumo solves an issue we often see in viticulture where individual valves are spread throughout the vineyard. In the past, this arrangement made automation expensive given that each valve needed its own telemetry device, which typically starts at around $1800. If all your valves are located at one central location, you may have automated years ago because one device can service a handful of valves. Single Lumo valves clock in under half of this price tag, so it’s a good option for when you have valves scattered around the farm.
What Lumo hangs its hat on though is its continued monitoring of water usage and fluctuations in flow. This allows for precise applications of water to each block as well as keeping a lookout for leaks and blowouts. For a lot of growers who have used Lumo, there tends to be a big discrepancy between how much they thought their output would be and what it is.
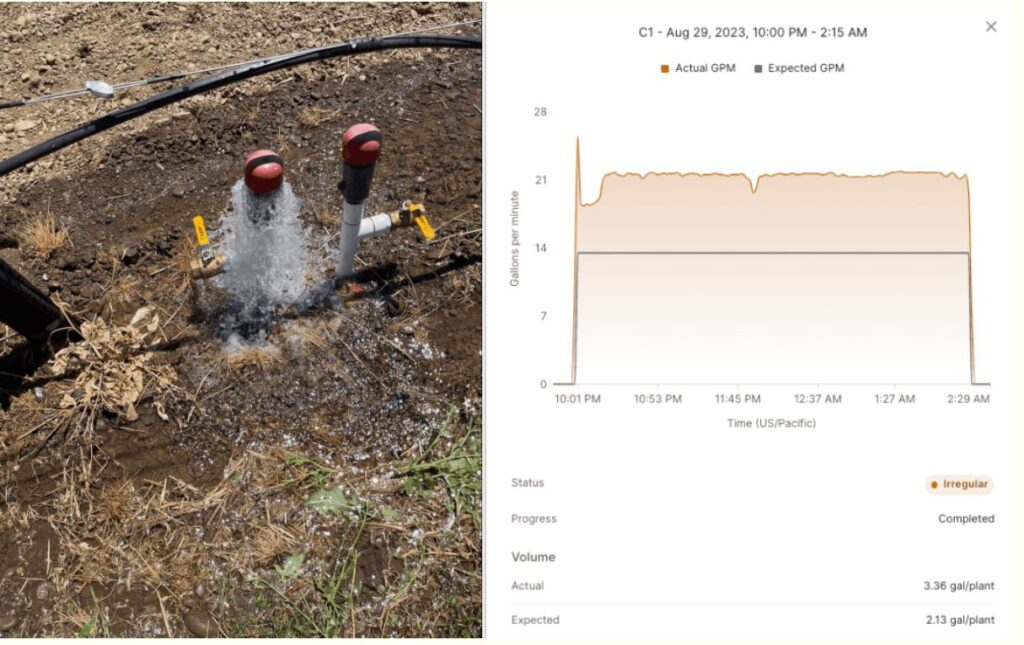
Kick the tires
Will automation work in your vineyard? The best way to determine that is to have a qualified irrigation professional assess your system. Here at Advanced Viticulture, we partner with irrigation specialists throughout California to ensure that you put your best foot forward in any project. As Saul said,
“Automation is not going to fix a poorly designed system. You need to understand how your system works and make sure that it’s designed properly to handle an automation system on it. We’re honest with customers. We’re not going to sell them a system if we know it’s going to fail. We’ll say, hey, you need some upgrades to do before any automation to work here. I would say that’s a really important thing that sounds like common sense, but I’ve seen some stuff out there that had no business being installed.”
For the most part, no automation company, Lumo or otherwise, wants the application of their equipment to fail. Dissatisfied customers are infinitely more vocal than satisfied ones. It’s one of the reasons Lumo works with companies like AvidWater and Advanced Viticulture to make sure their product is a good fit for each system prior to installation. Regardless of what company you go with, ask around. Ask the company selling you the devices to put you in touch with an irrigation expert. Then plan your budget accordingly. You may need to do some work on your infrastructure first and put off automation for a year or two. That’s still better than getting stuck with an expensive system that doesn’t work.